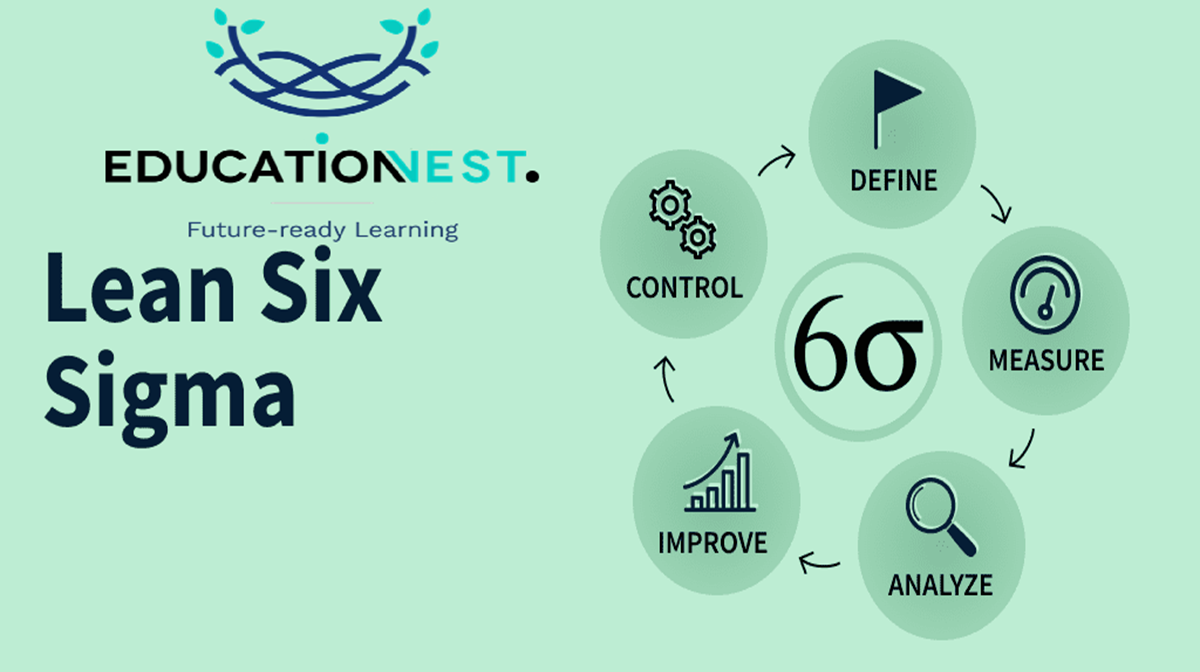
Companies use different methods today to achieve their goals. There is no shortage of methods available today for companies to choose from. But if there was one tool that stood the test of time, even when all the industries evolved over the years, that is Lean Six Sigma. It is a powerful method for process improvement that boosts efficiency and cuts down on defects. Green Belt happens to play a big role as it proves an individual’s grasp of Lean Six Sigma techniques. This blog explores examples of Lean Six Sigma Green Belt projects and explains why they matter.
What is Lean Six Sigma Green Belt All About?
The Lean Six Sigma is made up of two principles – Lean focuses on cutting waste and
Six Sigma aims to reduce variation and boost quality.
Lean Six Sigma is a powerful combination of these two for improving processes. Now what is Green Belt? It is simply a certification that plays a big role in validating a professional’s understanding of Lean Six Sigma. There are various belts – from yellow (for newbies) to green and black (for project leaders). Lean Six Sigma training is essential to crack this level and get a Green Belt.
Companies That Benefitted from Lean Six Sigma Green Belt
If you are thinking that Lean Six Sigma training is really what you need, let us show you some real facts. Here are some examples of real-life companies that tasted success after implementing the Lean Six Sigma Green Belt.
Wipro
Wipro, a major tech company in India, was known for its work in consumer goods but struggled severely with customer service. In 1995, when Wipro started thinking of global expansion with its software, it had to make some changes. Azim Premji, the chairman, realized that to compete internationally, Wipro needed to improve its quality practices. When Wipro teamed up with General Electric to develop ultrasound devices, they saw how GE successfully used Six Sigma. Premji believed that Wipro could also benefit from adopting this approach in their IT division.
The results:
- Adopting Six Sigma at Wipro brought quick and noticeable benefits. Software defects were cut by 50%, and rework on software dropped from 12% to 5%
- Productivity jumped by 35%
- In hardware, installation failures fell from 4.5% to just 1%
Boeing
In 1990, when Boeing saw a demand to increase the pace of production of planes, they realized they did not have either the required pace or the skilled staff to keep up. It was at this time that they adopted Lean Six Sigma by taking help from Toyota, which was a leader in Lean manufacturing. The key tools they used included ey tools including Value Stream Mapping, LDBR (Lean plus Design-Build Road Map), and Lean Tool Kit. Boeing’s executives received daily training from Toyota’s top coaches, and the transition took 10 years.
- Boeing increased its plane production by 4 times, producing 42 Boeing 737 aircraft per month, while reducing production area and workforce size
- According to Ray Corner, head of commercial planes, Lean Six Sigma boosted production rates by 60%, cut assembly time by 50%, and improved warehouse utilization by 132%
- Quality assurance costs dropped by 55%, and production area decreased by 41%
- For the Boeing 777, assembly time was reduced by 14%, warehouse turnover increased by 32%, engineering quality improved by 30%, and quality assurance costs fell by 10%
Microsoft
Microsoft’s experience with Six Sigma is a notable success story. They became a model for Six Sigma implementation by improving their Sharpe software among other products. In the mid-90s, Microsoft faced intense competition from Apple. This period also marked the rise of the Internet, creating new opportunities and challenges for IT companies. Microsoft had to rethink its strategy to meet the demands for high-quality IT products. They shifted their focus towards developing web-based software solutions for both consumers and businesses. Microsoft targeted eight key areas for waste reduction: unnecessary movement, excess inventory, non-essential procedures, delays, overproduction, defects, and underused staff skills.
- This approach led to the development of the Windows CE OS platform, which was highly successful and compatible with various devices like TVs and PDAs.
Green Electric
General Electric was struggling with product quality and service despite hiring top-quality professionals in their workforce. In 1995, CEO Jack Welch aimed to make GE a Six Sigma company within just 5 years. He required all employees to undergo a 2-week, 100-hour Six Sigma training. Furthermore, all employees were given a deadline to complete a certified Sigma project by 1998. Employees also needed Six Sigma Green Belt certification to get promoted.
- By 1997, GE saw nearly $700 million in benefits from Six Sigma, and by 2000, this figure rose to over $2.5 billion.
- Improved product reliability and production efficiency boosted customer satisfaction and revenue.
Conclusion
In conclusion, Lean Six Sigma Green Belt certification is crucial for companies wanting to beat their competitors. Beyond the examples discussed, there are many other companies that have successfully implemented Lean Six Sigma techniques to bring value to the industry. In fact, many companies view Lean Six Sigma certification as a prerequisite for promotion.
Hence, if you are trying to get into higher roles at your company, a Green Belt can significantly boost your chances. EducationNest offers comprehensive training programs in this area with expert-led trainings and course materials that are accessible throughout your lifetime. If you are someone fearful of taking the leap, check out their Lean Six Sigma Green Belt course today!